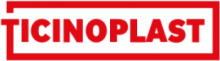
Based in Pogliano Milanese for over 50 years, Ticinoplast extrudes blown polyethylene film for food, medical and industrial packaging. The company is recognized as one of the most innovative in the flexible packaging market. Ticinoplast SpA has a production capacity of over 15,000 t/y, sells both in Italy and abroad and is ISO9001, BRC GS Packaging Materials and ISCC PLUS certified. The knowledge of converting processes - especially printing laminating and packaging manufacturing - and of the different packaging machines, allows Ticinoplast to provide customers with the most performing films.
The growing attention to environmental issues and sustainability has led Ticinoplast to develop products in line with the principles of circular economy: films designed for the realization of mono-material, compostable and renewable packaging, with and without gas and aroma barrier.
In the last few years Ticinoplast has focused on solutions to reduce the weight of packaging by reducing thicknesses (more technical films) and densities (expanded films).
Through important international industrial agreements Ticinoplast has also been developing for some years now recyclable and compostable mono-material packaging solutions that in the near future will be the most requested by the market; in fact, the major food multinationals have set 2030 as the date by which all their packaging must meet these requirements.
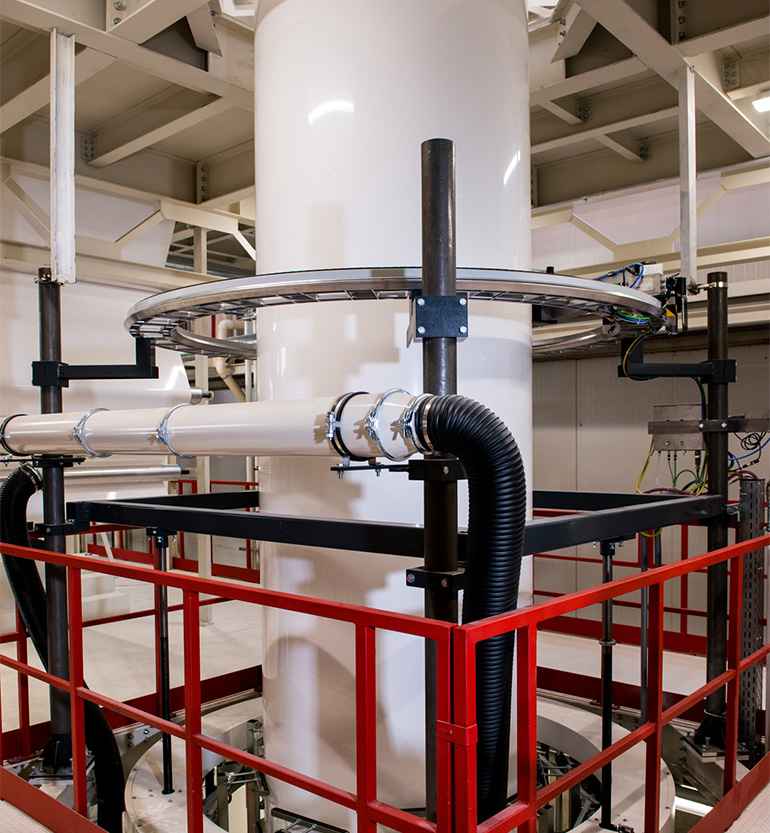
Settori di destinazione
Merceologia
- 1.A. MATERIALS AND AUXILIARY PRODUCTS
- 1.A.3. Plastic
- 1.A.3.11 Biobased films
- 1.A.3.13 Biodegradable films
- 1.A.3.16 Compostable films
- 1.A.3.18 Post-consumer recycled (PCR) films
- 1.A.3.34 Polyolefin neutral films: PE, PP, OPP, transparent, white, pearly, etc.
- 1.A.3.37 Special films: anticorrosives, antifog, etc.
- 1.A.3.40 Heat sealable films
Prodotti

Mono-material SOLUTIONS
Post-consumer recycling of flexible packaging is mostly done through mechanical recycling or chemical recycling processes. Mechanical recycling has the lowest energy consumption, enhances the value of single-material packaging and produces sub-products suitable for plastic films destined for non-food sectors such as co-commodities, detergents, shrink-wrap and stretch wrap. The most suitable chemical recycling process uses the pyrolysis-hydrogenation cycle to produce raw materials suitable for food contact.
Which is why Ticinoplast, together with its international partners, has focused on the development of bi-oriented polyethylene films, suitable both for printing processes and for finishing with coating or vacuum processes that guarantee barrier properties against gas, aromas and water vapor. The production of bi-oriented films takes place on lines that produce up to 40-50,000 t/y, ensuring the industrial availability of the same. The solvent or solventless lamination of these bi-oriented films, available in different densities with high optical and mechanical properties, to blown film with high sealing properties, allows the formulation of almost all the structures now required for optimal food preservation.
Monofilm bags up to complex triple and/or quadruple complex packs can be made, even using expanded films to reduce their overall weight; all the while maintaining the percentage of mono-material greater than 95%, as required by market standards. These, in brief, are the objectives of the PEoneer® project, started in 2018, and which has reached the industrialization stage thanks to the installation of a dedicated line of 25,000 t/y in the plant of the partner involved in the initiative.
NEXTFILM™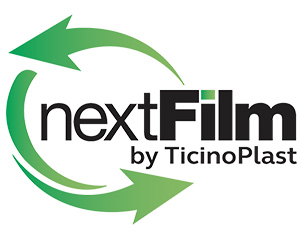
Sustainability in the packaging industry follows the 3Rs rule: recycle, reduce and reuse. Ticinoplast, with the launch in 2020 of its range of products called Nextfilm™, has focused on the research and production of new products that are more sustainable and closer to the concepts of circular economy: From compostable films, OK COMPOST certified, to films designed to produce “mono-material” laminates that allow 100% recycling, up to plastic films with weight reduction that mainly translates into a decrease in film density and therefore less use of plastic material, improving the competitiveness and sustainability of the product without affecting the mechanical and welding characteristics of the film itself.
In addition to the traditional lamination foams, Ticinoplast is also developing flexible films suitable for thermoforming, always composed of polyethylene foam laminated to PE (barrierated or not depending on the application), in order to offer the market an all PE flexible “bottom”. The recent achievement by Ticinoplast of the ISCC PLUS certificate, also allows the production of films with resins from chemical recycling suitable for food contact and films of biobased origin.
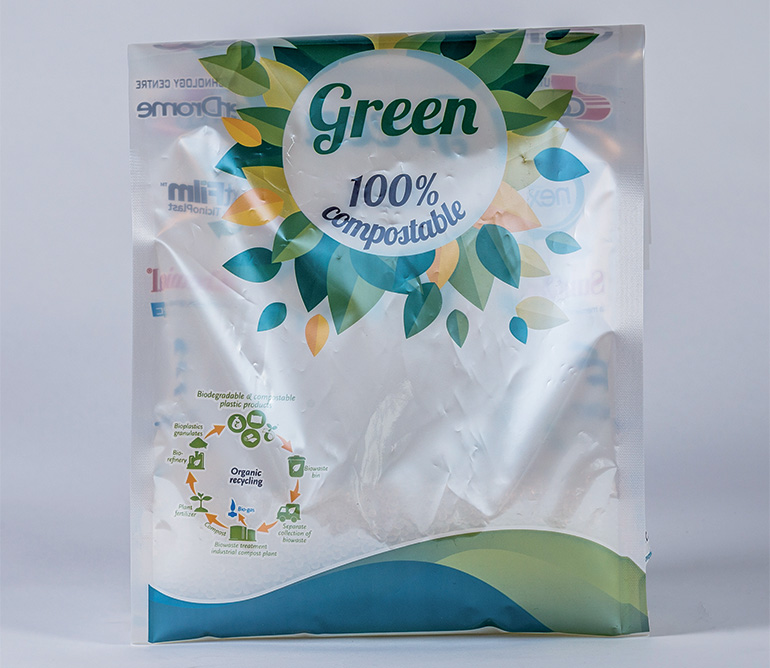